
Recently I spoke at a sign industry forum where the topic was how shops achieve higher levels of throughput and improve on-time performance. I touched upon value stream mapping, wait times and scheduling, batch manufacturing, functional cross-training, and lean principles.
At the end of my presentation, I collected the audience satisfaction surveys and went through them to see where I could improve my presentation. I was intrigued by one comment in the form of a question that asked, “Why did you skim over 5S?”
At first, I thought to myself, “That’s odd. Isn’t 5S common knowledge? Why should I spend so much time on it?”
I assumed wrong—what I learned is most people have heard the term “5S,” but very few really know what it’s all about and even fewer implement it successfully.
It turned out to be a great question. What’s interesting is that the person who asked the question was Steve Watts, president of Image National Sign Co., in Boise Idaho. Myself and twenty-plus other professionals were about to tour his facility that same afternoon.
I did not realize it at the time, but I was in for an experience that was delightful and inspiring because Image National hit a home run with their 5S implementation.
The factory floor was immaculate in its cleanliness. It was bustling with activity. There was no chaos, and the staff was happy, relaxed [no stress], and all working together as a cohesive team producing at the highest level and setting the bar way above any of the competition.
So I thought this would be a fantastic opportunity to share what can be gained when a successful Lean 5S program is implemented. It’s not rocket science folks—just a common-sense proven practice.
One of the core elements of the lean philosophy is eliminating waste to maximize flow. There are eight forms of time-consuming activities labeled by 5S as “wastes” that do not bring value to our people, our products, or our customers: (1.) Defects, (2.) Overproduction, (3.) Waiting, (4.) Non-used Skills, (5.) Transport, (6.) Inventory, (7.) Motion, and (8.) Excess Processing. An easy way to remember what they are is the acronym DOWNTIME.

Graph #1 illustrates what one of my clients accomplished over a twenty-four-week period of time utilizing this strategy—a 34 percent reduction in production turn-around time from an average of fifty-nine days to less than twenty days. (Note: This was for custom design-build projects. If you manufacture a predefined product line, you should be able to achieve even greater results.)
What is 5S?
5S is one of the many tools in the Lean methodology toolbox. It is a workplace organization process designed to make work environments more efficient and effective—in other words, faster!
The name 5S is derived from the five stages of this lean methodology originating from Japanese automakers during their post-WWII economic rebuild. Each of the five stages starts with the letter S, hence the term “5S,” as discussed below.
How Does 5S Work?
To implement 5S, you will have to follow the five stages in sequence, as described shortly, that make up the process. It really is that simple. However, be informed; simple does not necessarily mean easy!
You must be committed to following through to completion, even though you are never really done. You should be constantly cycling through the process as part of an ongoing process improvement culture.
Stage 1: Separate [and Sort]
Many shops are filled with “stuff” that is rarely, if ever, used. Workers simply tend to collect things that are non-value add.
Within this first stage, you will begin with what is called a Gemba walk (waste walk) to determining which tools/materials are actually necessary.
Select an area to start and begin placing tags or stickers (commonly known as red tags) on every item that is not required for the operation, is not in the right place, or is not present in the right quantities.
All these items are then transferred to a central staging area known as the “red tag zone.” They can only leave this zone when a person can and will actually use them. This way, items are redistributed to an area or workstation in which they are needed. Items that are not required after a certain amount of time, say sixty days, should be sold, removed, recycled, or disposed of.
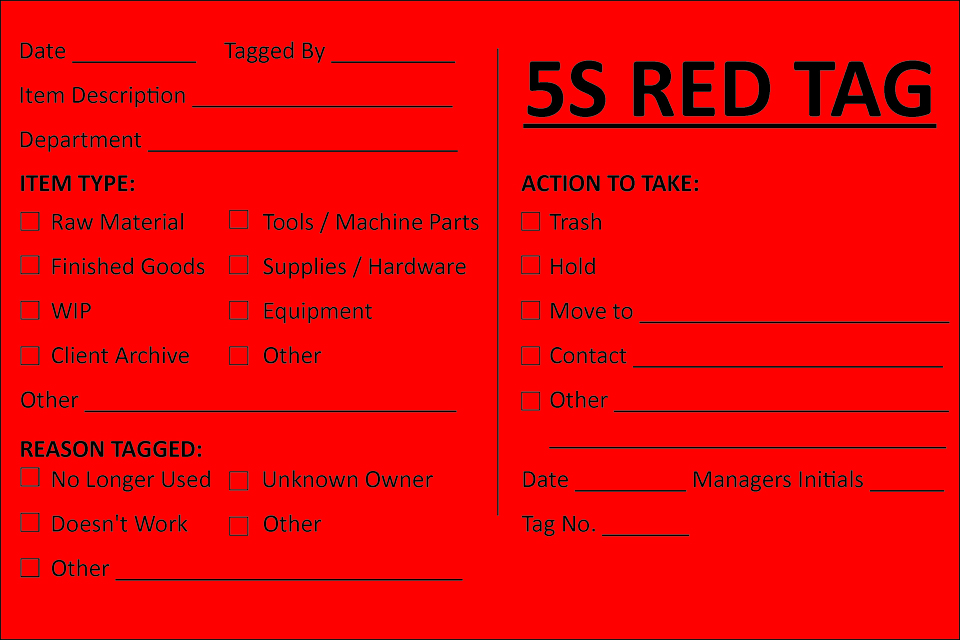
Stage 2: Set [Arrange and Organize]
In this stage, you give tools, supplies, and materials a permanent place in your shop.
First remove every single remaining item (left over from Stage 1) and place it a short distance away. Then categorize the items based on their frequency of use (whether it be hourly, weekly, monthly, and yearly), but feel free to create categories that suit your own needs.
After this categorization process, you place the most frequently used tools, supplies, items, etc., the closest to the place where they are consumed or processed. The other items are placed further away.
Now that you’re items are in the right spots, you’ll need to make sure they stay there and will be put back, in the same place, after they are used.
The use of a Visual Management aide such as a shadow board (painted board with each tool clearly labeled with lines drawn around them) is an effective way of organizing.
The goal of marking the location for each and every tool on the board is to make it really obvious when a tool is missing, which in turn should decrease the possibility of productivity loss because something is missing that is necessary for the operation. Within seconds (no more than three), anyone passing by should become aware as to whether something is out of place. This is referred to as the three-second rule.
Stage 3: Shine [Clean]
This third stage is an activity that employees would be either partly or completely responsible for, depending on the nature and scale of your operation.
One of the biggest advantages that comes from having operators regularly cleaning their assigned machines and/or workstations is that the operators are more likely to discover small abnormalities that happen to emerge in use, before they result in producing defects.
This means that the goal of the Shine [Clean] stage is not just cleaning a machine but setting the stage for the practice of operators responding to deviations from the standard, which is the most important practice within lean thinking and behaving.
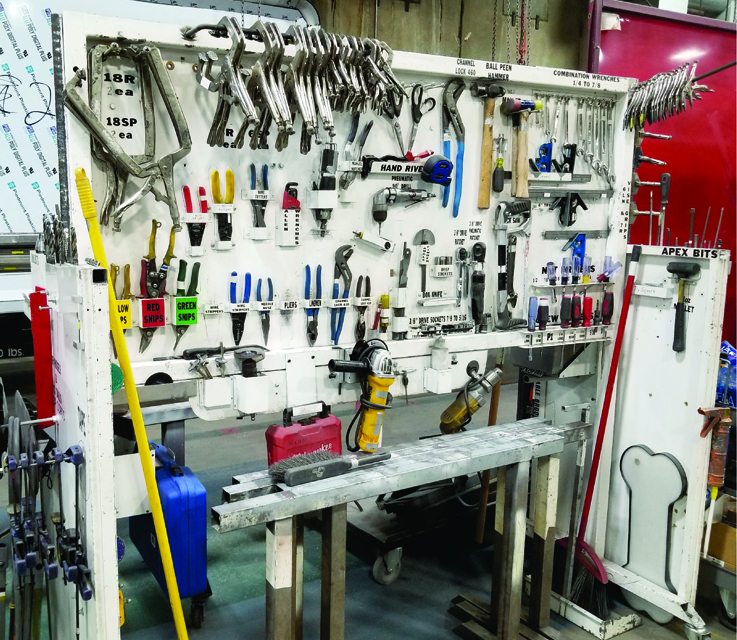
Stage 4: Standardize
In the standardize step, you will work on creating a consistent approach to the way tasks work and procedures are executed. The first goal is to set ground rules for how work is to be performed at the work center in which 5S tasks are integrated in the regular process flow.
The second goal is all about prevention. Set up clear rules to prevent accumulation of unnecessary items, breakdown of procedures, and prevention of contamination of machines or materials. Build infrastructure and set up rules that make sure you meet these two goals.
Stage 5: Sustain [Hold on to Changes]
The last stage is the most difficult one of the 5S methodology. Holding on to the changes made is not very straightforward because learned behavior is competing with new behavior.
Maintaining the previous four stages and making a habit out of them is the goal of Sustain. People are hesitant to change and altering set behavior can be difficult. So be ready to reinforce the new “good” behavior.
To make it easier, there are many things you can do. Try documenting routines and standard operating procedures or creating newsletters or guidebooks. Have team and management audits and schedule stand up meetings to ensure you and your team will hold on to the changes made!
Conclusion
The 5S process will only be successful if there is 100 percent commitment from upper management and a complete buy-in from all employees. Everyone needs to know why it’s important to eliminate the time wasters that limit flow and cause so many problems, as well as how to implement the process.
Companies fail 5S because they don’t understand the goal, thus sustainability is sacrificed. They find reasons to stop doing all the things I’ve outlined in this article.
Soon the benefits are mostly gone, people forget what it all means, and throughput drops, lead times rise, and so does cost. Worse they start losing skilled people because the culture suffers.
Lean 5S is one of the most powerful management strategies that typically yield the biggest return on your investment, especially at the onset of a Lean transformation initiative. The benefits you can expect to achieve will be greater on-time performance, less stress, and improved employee satisfaction; less firefighting for managers; an improved customer experience; and, best of all, more money in the bank!
John Hackley, ASBC, has thirty-five years of management and manufacturing experience and is Chief Efficiency Officer for Oculus Business Solutions, Inc. Reach him at [email protected]. John will be talking more about this month’s subject at the SBI/NSSA Northeast Conference & Expo being held at the Rhode Island Convention Center in Providence, Rhode Island.