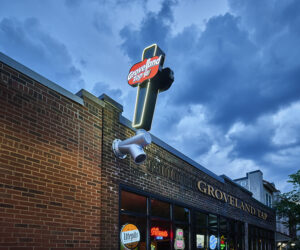
Let’s learn how one Minnesota pub tabbed a couple of sign companies to put together a recipe of sign making ideas to come up with a new exterior identity sign combining HDU and illumination with a beer tap theme.
Groveland Tap is a long-time “beer-and-burger joint” that’s located in the heart of the Mac-Groveland neighborhood, near Macalester College and the University of St. Thomas, in St. Paul, Minnesota. Inside the premises, you’ll find pub grub, a pool table, a jukebox, and a large array of tap beers.
The establishment had undergone some recent renovations and expansion over the past year, yet there was still a buzz to invest in some kind of new signage.
Craig Hassell, general manager of Groveland Tap, happened to be on vacation in Colorado when he came across a draft beer tap-inspired exterior sign being used. Hassell immediately knew that he wanted something similar for his pub.
He reached out to custom-focused Albrecht Sign Company of Fridley, Minnesota, to work on ideas for an identity sign at Groveland Tap. Their design idea featured a combination of formed components, channel letters, digital prints, and lighting all put together to resemble a large beer tap handle that would be mounted to the outside front façade of the Groveland Tap pub.
In turn, Albrecht Sign Company sent these renderings to Quality Manufacturing, one of the largest wholesale manufacturers in the Midwest, to handle the custom build.
The Quality Manufacturing designers and fabricators collaborated to make sure that the finished sign would fit the needs of the client and be properly engineered.
“We enjoy working with our clients to bring their visions to life,” says Shari King of Quality Manufacturing, “and we embrace challenges.”
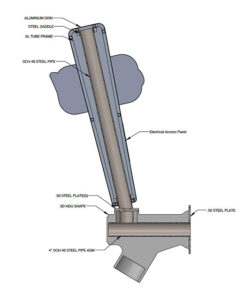
The overall footprint of the new beer tap sign measures 85.8 inches tall-by-47.5625 inches deep-by-16 inches wide.
The top 60.25-inch tap handle weighs 105 pounds and was built off a 1-by-1-by-0.125-inch aluminum square tube frame. Quality Manufacturing rolled this frame to the tap shape using steel saddles on both the top and bottom.
Both sides of the tap handle feature identical designs. Its faces are .125 aluminum, and the rolled side skins are .080 aluminum. Each face features channel letters Quality Manufacturing welded together with an IPG laser welder.
Quality Manufacturing output the first-surface Groveland Tap logo digital print applied to the channel letters using their EFI VUTEk GS3250 Pro hybrid roll-to-roll/UV LED flatbed printer.
The company trim-capped each face with one-inch GemTrim.
Quality Manufacturing used Hanley KS2100 LEDs to illuminate the channel letters, hooking them up to a Hanley H60W-PPS5 power supply.
Meanwhile they used white Allanson AFB1-032CW-24v-W-S-11 border tubing with an Allanson CV244-120/270 power supply to provide the lighting around the perimeter of the tap handle.
The formed 179.5-pound tap spout was constructed by gluing pieces of 1.5-inch HDU to a total thickness of 7.5 inches then 3D milling both the inside and outside of the spout on a Shop Sabre IS 612 CNC router. The inside of the HDU was milled to wrap around the inner steel frame.
According to the company, this was their biggest fabrication challenge—being that the sign was a double-sided piece.
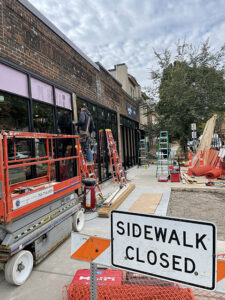
“With the use of our Solid Works 3D software, our design team was able to create the parts that had to be able to flip on the CNC table and match them up perfectly to fit around the steel framework,” says Ken Albrecht of Quality Manufacturing. “This [method] takes a longer initial setup time than a standard job, but having all the parameters figured out on the front end in the design process saves [us] time in the long run.”
The steel frame used for the entire sign consists of 4-inch schedule 40 steel pipe tubes and 0.5-inch steel plates. Quality Manufacturing MIG-welded all the frameworks (both steel and aluminum) using Miller P350 welders.
It was time to make a connection between the two pieces! The steel for the tap handle was attached to the steel from the spout using plasma-cut .50 match plates. It tips away from the building 15 degrees where the spout and the handle meet.
Quality Manufacturing painted the aluminum skin pole cover of the tap handle, as well as the tap spout, using Matthews MAP-LVS 202 White and Matthews MAP-LVS 923 Black paints.
Albrecht Sign Company picked up the one-piece sign to install it at Groveland Tap. They used their lift and ladders to attach the sign to the wall with the aid of a 16-by-0.5-inch steel plate. The installers followed a provided pattern of the mounting plate, pre-drilled and epoxied in anchors.
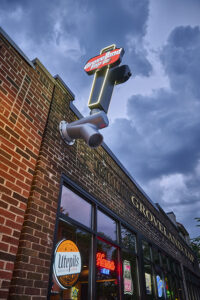
“Once the epoxy set up, the sign was then slid into place and bolted down,” says Albrecht. (Note: The electrical for the sign illumination was fed out of the center of the mounting plate to the building.)
Featuring almost four feet of projection off the building, the overhead, oversized beer tap handle sign provides customers below with an instant conversation piece. “The tap handle exemplifies exactly what people come to expect from us when they visit,” says King.
And Groveland Tap has been just as ecstatic over this refreshing new addition to their building. “We loved the sign when it arrived,” adds Hassell, “and we still do!”